Sputterziel sind Materialien, die für die Dünnschichtabscheidung verwendet werden.
Die Sputtertechnologie wird eingesetzt, um Materialatome oder Moleküle von festen Targets zu sputtern und anschließend dünne Schichten auf Substraten zu bilden.
Sputterziel werden häufig in der Elektronik- und Informationsindustrie eingesetzt, einschließlich Halbleiterchips, Solarzellen, Flachbildschirmen, Informationsspeicherung und anderen Bereichen.
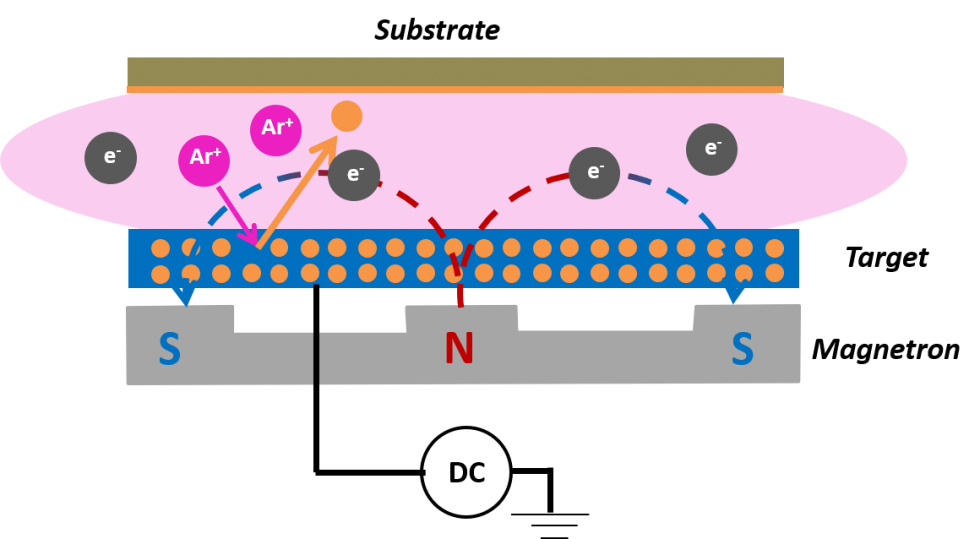
Ziel-Prozessablauf für Sputtern
Rohstoffpulver – Pulverschmelzen – Pulvermischen – Pressformen – Atmosphärensintern – Kunststoffverarbeitung – Wärmebehandlung – Ultraschallfehlererkennung – Wasserschneiden – Bearbeitung – Metallisierung – Bindung – Ultraschallprüfung – Ultraschallreinigung – Inspektion – Versand.
Unter ihnen sind die spezifischen Bedeutungen der Hauptprozesse wie folgt:
Pulverschmelzen: Das Rohmaterialpulver wird einem Vorsintern in Atmosphäre unterzogen, um den Gasgehalt im Rohmaterialpulver zu kontrollieren.
Pulvermischen: Das Zielmaterial hat eine einzigartige Formel, und der Gehalt jeder Komponente muss genau kontrolliert werden, und der Gehalt an Verunreinigungen muss streng begrenzt werden.
Bei der Pulvermetallurgie ist es notwendig, die Elemente gleichmäßig vollständig zu mischen, und die Partikelgrößenverteilung ist gleichmäßig, um eine Verschmutzung zu vermeiden, und ein gemischtes Verbundpulver muss mit speziellen Verfahrensmitteln hergestellt werden.
Pressformen: Das durch pulvermetallurgische Verfahren hergestellte Zielmaterial muss das Pulvermaterial vorpressen, um es zu einem Grünkörper mittlerer Dichte zu machen.
Die Gleichmäßigkeit der Dichte und die internen Defekte beeinflussen die Ausbeute des Hochtemperatursinterns in der späteren Phase.
Atmosphären-Sintern: Der vorgepresste Grünkörper muss einem oder mehreren Hochtemperatursintern unterzogen werden.
Je nach Material werden unterschiedliche Sintertemperaturkurven ausgewählt, und es werden unterschiedliche Sinterumgebungen, wie z. B. Sinteratmosphäre und Sinterdruck, ausgewählt, um Target-Rohlinge mit hoher Dichte herzustellen.
Kunststoffverarbeitung: Der Metallknüppel muss einer großen plastischen Verformung unterzogen werden, um ausreichende Längen-, Breiten- und Dickenabmessungen zu erhalten und die inneren Körner einer ausreichenden Zugverformung zu ermöglichen, wodurch genügend Versetzungen im Inneren erzeugt werden.
Wärmebehandlung: Nachdem der Metallknüppel eine große plastische Verformung durchlaufen hat, wird der Wärmebehandlungsprozess entsprechend den Eigenschaften der verschiedenen Materialien ausgewählt, so dass das Metallmaterial rekristallisiert und die innere Spannung des Materials beseitigt werden kann.
Ultraschall-Fehlererkennung: Nachdem der Zielrohling bearbeitet wurde, müssen Ultraschallwellen verwendet werden, um zu überprüfen, ob sich im Material Fehler befinden.
Nachdem der Target-Rohling mit der Rückplatte verklebt wurde, muss ein Wasser-Immersions-Ultraschallscanner verwendet werden, um die Bonding-Schicht zu erkennen und zu überprüfen, ob der Bonding-Bereich der Norm entspricht.
Mechanische Bearbeitung: Der Zielrohling muss durch eine präzise mechanische Umformung bearbeitet werden.
Die in Kombination mit dem Zielrohling eingesetzte Rückplatte muss aufgrund ihrer präzisen Abstimmung mit der Beschichtungsanlage und der Hochdruckwasserkühlung eine extrem hohe Maßgenauigkeit und mechanische Festigkeit aufweisen.
Die Verarbeitungsschwierigkeit ist relativ hoch, insbesondere bei der Rückplatte mit einem internen Umlaufwasserkanal.
Aufgrund der Besonderheit des Materials ist das geschlossene Schweißen des Wasserkanals sehr schwierig und erfordert ein spezielles Schweißverfahren.
Metallisierung: Bevor der Targetrohling und die Rückplatte gebunden werden, muss die Schweißoberfläche vorbehandelt werden, um die metallbenetzungstechnischen Eigenschaften des Targetmaterials und des Targetmaterials und des Lots zu verbessern, so dass eine Übergangsschicht auf der Oberfläche plattiert wird.
Bindung: Die meisten Zielmaterialien können aufgrund der physikalischen oder chemischen Eigenschaften des Materials nicht direkt für die Beschichtung installiert werden.
Metalllot wird benötigt, um den Zielrohling und die Rückplatte miteinander zu verschweißen, und die effektive Bindungsrate der Oberfläche muss eine großflächige Schweißgenauigkeit von mehr als 95 % erreichen.
Der gesamte Prozess muss unter hohen Temperaturen und hohem Druck durchgeführt werden.
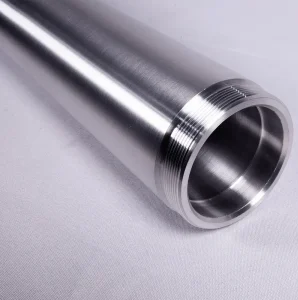
SPUTTERZIEL - HERSTELLUNGSPROZESS
Der Herstellungsprozess von Targets beginnt mit einem einzigartigen Prozessdesign, das auf die Leistung und die Anforderungen der beabsichtigten nachgeschalteten Anwendung zugeschnitten ist. Dieser Prozess umfasst wiederholte plastische Verformung und Wärmebehandlung, gefolgt von mechanischer Bearbeitung, Reinigung, Trocknung und Vakuumverpackung.
Zu den vorherrschenden Präparationsmethoden für Sputterziel gehören derzeit das Gießverfahren und das pulvermetallurgische Verfahren.
Vorbereitungsprozess Allgemeine Typenmerkmale | ||
---|---|---|
Schmelz- und Gießverfahren | Vakuum-Induktionsschmelzen Vakuum-Lichtbogenschmelzen Vakuum-Elektronenbeschuss Schmelzen |
Im Vergleich zur Pulvermethode weisen die durch Schmelzen hergestellten Legierungstargets einen geringeren Gehalt an Verunreinigungen auf, insbesondere in Bezug auf Gasverunreinigungen, und zeichnen sich durch eine hohe Energie und Dichte aus. Bei Legierungen, die Metalle mit sehr unterschiedlichen Schmelzpunkten und Dichten enthalten, ist es jedoch in der Regel schwierig, eine einheitliche Zusammensetzung der geschmolzenen Legierungsziele zu erreichen. |
Verfahren der Pulvermetallurgie | Heißpressen Vakuum-Heißpressen Heißisostatischer Druck (HIP) |
Durch diese Methode wird eine gleichmäßige, feinkörnige Struktur erreicht, die auch die Rohstoffe schont und die Produktionseffizienz erhöht. Zu den kritischen Faktoren gehören: die Auswahl von hochreinem, ultrafeinem Pulver als Rohmaterial, der Einsatz von Formungs- und Sintertechnologien, die eine schnelle Verdichtung ermöglichen, um eine geringe Porosität des Targets zu gewährleisten und die Größe der Kristallisationspartikel zu kontrollieren, sowie eine strenge Kontrolle der Einführung von Verunreinigungen während des Vorbereitungsprozesses. |
Extrusionsprozess | Heißextrusion Kaltfließpressen Warmextrusion | : Wird hauptsächlich zur Vorbereitung von rotierenden Zielen aus Metallen und Legierungen mit guter Plastizität verwendet, wie z. B. Aluminium-Kupfer-Zink-Nickel-Chrom-Legierungen. |
Plasmaspritzverfahren | Vakuum Wasserstabilität Gasstabilität Plasmaspritzen | Wird hauptsächlich zur Vorbereitung von spröden Metall- und Legierungskeramikzielen wie Metallchrom, Silizium, Silizium, Aluminiumlegierung, Oxid und anderen rotierenden Zielen verwendet. |
Die VI HALBLEITERMATERIAL GmbH bietet ein umfangreiches Sortiment an hochreinen, leistungsstarken Sputtertargetmaterialien, die in verschiedenen Formen und Zusammensetzungen erhältlich sind. Unser Bestand umfasst zirkuläre Sputtertargets, rechteckige Sputterziel, dreieckige Sputterziel, planare Sputterziel, rotierende Sputterziel und Ringsputterziel mit Reinheiten zwischen 99,0 % und 99,9999 %.
Die meisten Sputterziel können auf der Grundlage der zur Verfügung gestellten Zeichnungen in jeder beliebigen Form und Größe hergestellt werden. Für Sputtertargets mit technischen Einschränkungen hinsichtlich der maximalen Größe eines einzelnen Stücks können Segmente mit Stoß- oder Winkelverbindungen zu einem Sputterziel mit mehreren Segmenten verbunden werden.
Sollten die benötigten Sputterziel-Materialien/Spezifikationen nicht aufgeführt sein, bitten wir Sie, uns zu kontaktieren.
Was können wir Ihnen bieten?
Metall | Legierung | Oxid | Keramik (Nicht-Oxid) | Chalkogenid | Edelmetall | Seltene Erde | Halogenid | Verbindung |
---|---|---|---|---|---|---|---|---|
Al | AlCo | Al₂O₃ | AlN | Bi₂Te₃ | Ag | Ce | CsI | ATO |
Ba | AlCr | AlON | B₄C | BiSbTe | AgCr | CeGd | InF₃ | AZO |
Bi | AlCu | CdO | BN | BiSbSe | AgCu | CeSm | LiF | FTO |
Co | AlMg | Cu₂O | Cr₂AlC | CdS | Au | Er | MgF₂ | IGZO |
Cu | AlNi | Fe₃O₄ | CrSi₂ | FeS | Ir | Gd | PbCl₂ | ITO |
Fe | AlSi | Ga₂O₃ | GaN | GeS₂ | IrMn | La | YbF₃ | IZO |
Ge | CoCr | HfO₂ | MgSi₂ | MoS₂ | Pd | La₂O₃ | KF | YSZ |
Hf | CrNb | In₂O₃ | Mo₂C | MoSe₂ | PdAg | La₂Zr₂O₇ | ZnF₂ | ZTO |
Unter | CrSiAl | Li₂O | MoSi₂ | NbSe₂ | PdNi | LaB₆ | MoCl₅ | BaTiO₃ |
Li | CuSn | MoO₃ | NbN | SnS₂ | Pt | Sm | NbCl₅ | BaVO₃ |
Mg | CuZn | Nb₂O₅ | Si₃N₄ | ZnS | Rh | SmB₆ | ZrF₄ | BiFeO₃ |
Mn | FeCrAl | NiO | SiC | CdTe | Ru | SmCo | … | BiVO₄ |
Mo | MoNb | Sb₂O₅ | TaC | ZnSe | … | Tm | KNbO₃ | |
Nb | MoTa | SiO | TaN | ZnTe | Y | Li₃PO₄ | ||
Ni | MoW | SiO₂ | Ti₃SiC₂ | CaSe | Yb | LiCoPO₄ | ||
Sb | NbTi | SnO₂ | TiB₂ | FeSe | Yb₂O₃ | LiSiO₄ | ||
Sc | NbZr | Ta₂O₅ | TiN | Cu₂Te | YBCO | LiFePO₄ | ||
Se | NiAl | TiOx | VN | CuTe | YPO₄ | MgTiO₃ | ||
Si | NiCr | V₂O₅ | VSi₂ | NiTe | … | MgSiO₃ | ||
Sn | NiFe | ZnO | WC | MoTe₂ | SrTiO₃ | |||
Ta | NiSi | ZrO₂ | WSi₂ | … | SrNbO₃ | |||
Te | NiV | … | ZrB₂ | ZnTiO₃ | ||||
Ti | SiFe | ZrC | ZrNbO₃ | |||||
V | TiAlSi | … | … | |||||
W | TiZr | |||||||
Zn | WRe | |||||||
Zr | WTi | |||||||
… | ZnSn | |||||||
… |